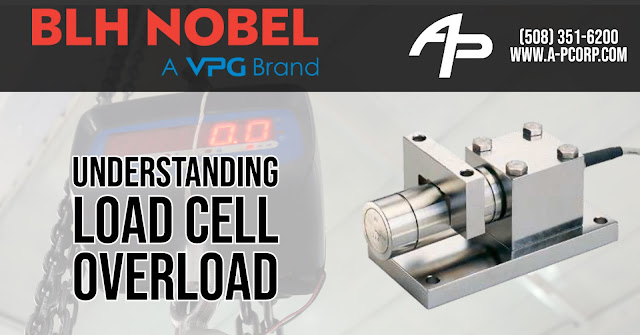
When you're talking about load cells in process weighing, what does safe and ultimate overload mean, and how strong are load cells?
The ultimate strength relates to the function as a load cell and not the mechanical strength. The mechanical strength of the load cell is even higher.
For a load cell, there is generally three capacity limits:
The nominal capacity of one 100%: Let's say we have a 100-pound load cell. This is the limit or capacity of the load cell. Note the load cell should not be subjected to higher forces under regular use. If the application needs to measure higher loads, then a larger load cell should be used.
The safe load usually is 200 percent of the rated capacity: Let's say with the 100-pound load cell this would be 200 pounds. If the load cell is occasionally subjected to more than 100 percent but less than 200 percent, nothing happens to it, and it will work. If repeatedly subjected to more than 100%, the load cell can be damaged due to fatigue.
The ultimate load is usually 300 percent of rated capacity or 300 pounds for a 100-pound load cell. If the load cell is occasionally subjected to a load greater than 200 percent but less than 300 percent, the load cell will be subjected to a zero shift. However, in most cases, the load cell can be recalibrated and repaired. If subjected to more than 300 percent, the bonding of the strain gauges will most likely be damaged beyond repair. The function of the load cell is damaged, and it should be scrapped.
As a reminder, this refers to the function as a load cell and not the mechanical part. The mechanical strength of a load cell varies but is often in the range of 400 to 1 000 percent. It should also be noted that there's a fatigue limit for a load cell that generally is 133 of capacity.